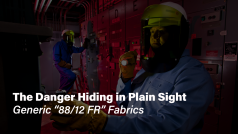
The vast number of flame resistant fabrics, garments and manufacturers in today’s market has led to confusion around the differences between flame resistant (FR) fabric types, FR fabric manufacturing methods and FR garment brands. Many don’t realize that the term “88/12 FR” is nothing more than a fabric content or type of fabric. “88/12 FR” is not a brand of fabric, and therefore does not provide any information on fabric performance, which varies widely by fabric manufacturer. It’s also not well understood that who manufactures the fabrics is almost always different from who manufactures the garment, and behind a trusted garment label might be lower-quality, generic FR fabric. Given the poor performance of generic “88/12 FR” fabrics, misunderstanding the terms and labels can have serious consequences for workers.
Understanding “88/12”: A Type of Fabric — and Nothing More
“88/12” is simply defined as a fabric blend with fiber content of 88 percent cotton and 12 percent nylon. The numbers “88/12” are unrelated to flame resistance, safety certification, durability, shrinkage, comfort or any other properties. In fact, an “88/12” fabric could even be a non-FR fabric. Even with the designation of FR added, “88/12 FR” still does not provide any information on the fabric’s flame resistant durability. An “88/12 FR” fabric might be soft but have poor flame resistance, or an “88/12 FR” fabric could have good flame resistant durability but be stiff and shrink excessively. Or an “88/12 FR” fabric may be manufactured through a high-quality FR engineering process that provides guaranteed flame resistance as well as a soft feel and excellent shrinkage control. Despite this large amount of variability, many fabric and garment manufactures use the term “88/12 FR” as way of saying “high quality and comfortable,” although there’s no relationship to the fabric properties.
Market dynamics muddy the waters
In the early 2000s, new regulations, market dynamics and innovations in flame resistant fabric came together to create a perfect storm of confusion surrounding flame resistant fabric.
Cotton has long been the preferred fabric among workers because of its lightweight, breathable and soft qualities. As early as the 1950s, research enabled cotton garments to be made flame resistant, though the science had only been applied to 100 percent cotton fabrics at the time. However, in the late 1990s, a flame resistant fabric brand made with 88 percent cotton/12 percent nylon high-tenacity blend was introduced (Westex UltraSoft®), which, through an innovative FR engineering process coupled with this new fabric blend, brought the benefits of high-tenacity nylon — significantly higher abrasion resistance which proved to increase the durability by over 75 percent when compared to all cotton. In addition, revolutionary new softening technology was utilized which dramatically increased the level of comfort. Many considered the new fabric groundbreaking, and the generic term “88/12” was widely communicated in conjunction with the benefits of this superior fabric. A few years later, the generic term “88/12 FR” mistakenly came to stand for all the qualities workers wanted in FR fabric — safety, comfort and durability — although it wasn’t the “88/12” fabric type that provided these properties, but the Westex UltraSoft® fabric brand made with 88 percent cotton/ 12 percent nylon.
Asian manufacturers exploit conditions
In 2010, the U.S. Occupational Safety & Health Administration (OSHA) instituted new regulations requiring upstream oil and gas industries to provide workers with flame resistant PPE for deadly flash fire hazards. As a result, demand for FR garments grew quickly, often overwhelming the supply chains of U.S. fabric manufacturers. Many Asia-based fabric manufacturers, using low-cost labor and engineering shortcuts, flooded the market to make a profit on this booming industry. Many of these manufacturers called their products “88/12 FR” to suggest a similarity to or “same as” the popular and trusted FR fabric brand launched a decade earlier. The idea that these flame resistant fabrics were all the same began to take hold.
“Any mill in the world can put 12 percent nylon in their blend,” says Mike Enright, Vice President of Westex by Milliken, a leading manufacturer of FR fabric. “But it doesn’t tell you anything about protective performance. We’ll hear people say ‘I know the fabric is important, so I went with 88/12.’ Or, ‘I switched from brand X to 88/12 FR.’ They don’t realize that there are vastly different levels of performance between various 88/12 FR fabrics.”
Differences across generic “88/12 FR” fabrics — and risks
End users would be right to think FR generics often look the same as name-brand FR fabrics. Different “88/12 FR” fabrics described on paper, or even just seen on a hanger, may appear and even feel similar. The fact is, important differences exist among all “88/12 FR” fabrics, such as durability of flame resistance properties, level of comfort, softness and shrinkage control. These qualities vary widely among all FR fabric types, including all of those made with 88 percent cotton and 12 percent nylon.
Since most generic “88/12 FR” fabrics are certified to various NFPA standards, it is misleading to compare and contrast fabric brands against these minimum standards.
The NFPA standards set a minimum level of safety requirements. There’s no doubt the standards save lives, but they are intended as a starting point and general guideline for organizations. For example, under NFPA 2112, it’s acceptable for flame resistant fabric to have less than 50 percent predictable second-degree body burn — but having close to half of your body burned can result in extended hospitalization and even reduce your chance of survivability. Many FR fabrics certified to NFPA 2112 consist of a wide range of body burn performance.
In fact, private testing has shown that some certified generic “88/12 FR” fabrics have poor performance across flame resistance (see graph). By contrast, an FR fabric brand made with “88/12” fiber content manufactured in the U.S. by a well-known, trusted company with advanced, proprietary engineering methods, state-of-the-art equipment and decades of experience not only meet standards — it exceeds them.
“The standards allow an ‘88/12 FR’ fabric to enter the playing field,” explains Enright. “But lots of NFL players make the draft, while only a small percentage make the team and a select few are star players. If you want the star player, we recommend specifying a brand of FR fabric from a company you know and trust — otherwise, you could be getting anything.”
Many generics force an unnecessary choice: safety, shrinkage or softness
The “88/12” label applied to so many generic fabrics also falsely suggests that these fabrics offer softness and shrinkage control, as well as FR. But there’s a relationship between long lasting FR, softness and shrinkage that’s closely tied to how these fabrics are engineered. Most fabric manufacturers struggle to manage all three without de-emphasizing one attribute or another. That’s because the flame resistance process — the retardant polymer added to the fibers — makes the fabric stiff and difficult to preshrink. But reduce the amount of flame resistance for softness, and the FR protection decreases. To achieve all three, and to even guarantee flame resistance, requires special preparation methods, customized equipment and multi-step engineering technologies. End users shouldn’t assume generic fabric manufacturers have these capabilities. Most only have experience manufacturing regular clothing, and they continue to use non-FR mills and equipment.
“You want these generic manufacturers to compromise in the softness and shrinkage categories — and most of them do,” says Enright. “But keep in mind that it’s hard to tell if they compromise on flame resistance. It’s not a quality you can see unless you physically test it, which destroys the fabric.”
Generic “88/12” Fabrics — Hiding Behind Garment Brands
How can poorly performing generic “88/12 FR” fabric be avoided? The fact is, poor-quality generic “88/12 FR” fabrics can be anywhere, even in the products made by well-known, FR garment brands. Some distributors benefit from the lower cost of generic fabrics that are quickly and cheaply manufactured — and there’s no requirement that the fabric source be made clear to the end user. The best and safest approach is simply to ask what brand of fabric is used when making buying decisions. Take an active role, and don’t settle for the response that “this brand is ‘88/12 FR,’” “‘88/12 FR’ fabrics are all the same” or “this fabric is the same as brand X because it’s ‘88/12 FR.’”
“I’ve worked in this industry for over two decades and I’ve seen first-hand what can happen to workers in arc flash and flash fire hazards if they are wearing garments made with the wrong fabrics,” says Enright. “So I can tell you, the FR fabric should be your first and most critical consideration. The fabric brand — not the garment brand — is where the majority of the engineering happens to make the garment protective.”
The information in this publication is based on testing conducted by or conducted on behalf of Westex, Inc., a subsidiary of Milliken & Company, and represents our analysis of the test results. It is not intended to substitute for any testing that may be unique and necessary for your facility for you to determine the suitability of our products for your particular purpose. Since we cannot anticipate all variations in enduser conditions, Westex, Inc. makes no warranties and assumes no liability whatsoever in connection with any use of this information. As each customer’s use of our product may be different, information we provide, including without limitation, recommendations, test results, samples, care/labeling/processing instructions or marketing advice, is provided in good faith but without warranty and without accepting any responsibility/liability. Any test results reported are based on standard laboratory testing but should not be used to predict performance in actual fire situations. Each customer must test and be responsible for their own specific use, further processing, labeling, marketing, etc. All sales are exclusively subject to our standard terms of sale posted at www.milliken.com/terms (all additional/different terms are rejected) unless explicitly agreed otherwise in a signed writing. Use caution near sources of flame or intense heat and do not launder with bleach or fabric softeners. Westex®, UltraSoft® and Milliken® are all registered trademarks of Milliken & Company.